USULAN PENERAPAN 5S PADA AREA KERJA UNTUK MENINGKATKAN PRODUKTIVITAS KERJA
(Studi Kasus Di Bengkel Body Repair Palembang)
Romiya 16.12.019, Fitra Bintang Bagus Trihantara 16.12.024 , Dwi Kurniawan 1612017
Prodi Teknik Industri, Fakultas Sains dan Teknologi
Universitas Katolik Musi Charitas Palembang
Email: 1.miawani17@gmail.com, 2.kucingmakan20@gmail.com, 3.dwiku.awan@gmail.com.
Abstrak
Bengkel Body Repair merupakan bengkel yang berfokus dalam memperbaiki body kendaraan khususnya roda empat. Temuan masalah di area kerja ada sisa-sisa material yang tidak dihilangkan dan peralatan yang berserakan sehingga ruang kerja sempit dan tidak ada manajemen dan pengawas yang mengatur lingkungan kerja dan keselamatan kerja. Penelitian ini bertujuan untuk mengimplementasikan rancangan 5S terhadap kondisi yang ada. Penelitian ini menggunakan metode kualitatif, yaitu metode 5S. Tahap seiri dirancangkan untuk memisahkan benda yang diperlukan dengan yang tidak diperlukan, kemudian menyingkirkan yang tidak diperlukan (ringkas). Tahap seiton dirancangkan untuk menyusun dengan rapih dan mengenali benda untuk mempermudah penggunaan. Tahap seiso dirancangkan untuk selalu membersihkan, menjaga kerapihan dan kebersihan (resik). Tahap seiketsu dirancangkan untuk terus menerus mempertahankan 3 S tersebut diatas, yakni Seiri, Seiton, dan Seiso. Tahap shitsuke dirancangkan untuk memotivasi pekerja agar terus menerus melakukan dan ikut serta dalam kegiatan perawatan dan aktivitas perbaikan serta membuat pekerja terbiasa mentaati aturan (rajin). Setelah diketahui penyebab yang paling dominan terhadap permasalahan, selanjutnya menentukan rencana penanggulangan terhadap permasalahan di Bengkel Body Repair agar dapat meningkatkan produktivitas
Kata Kunci: 5S, Produktivitas Kerja, Fishbone.
1. Pendahuluan
Bengkel Body Repair merupakan bengkel yang berfokus dalam memperbaiki body kendaraan khususnya roda empat. Dalam mengelola proses perbaikannya, pihak bengkel memberikan tanggung jawab kepada pekerja dalam melakukan perbaikan dan penyelesaian . Bengkel Body Repair merupakan salah satu bengkel yang menyediakan layanan body repair. Namun, hingga saat ini pihak bengkel masih menerima beberapa keluhan atas pelayanan yang diberikan. Salah satunya adalah kualitas hasil selesai perbaikan. Ratarata mengenai kualitas hasil yang membandingkan dengan bengkel body repair lainnya.
Palembang Body Repair adalah salah satu bengkel di Palembang yang memulai usahanya sejak tahun 2017 berlokasi di Jalan Pendawa 2ilir Lemabang. Dalam bengkel ini terdapat beberapa jasa yang di berikan pihak bengkel seperti repair mobil, repaint mobil atau cat mobil, salon mobil, dan pembuatan pencetakan variasi berupa bodykit mobil. Terdapat beberapa stal atau tempat dalam bengkel Palembang Body Repair mulai dari Stal perbaikan, stal dempul, stal cat, dan stal poles atau finishing mobil. Dari stal tersebut merupakan rangkain urutan proses perbaikan mobil atau repair pada mobil ketika mobil siap di repair dan adi proses dalam bengkel tersebut dari awal masuk hingga selesai. Kepuasan pelanggan menjadi sorotan oleh pihak bengkel karena hal ini akan mempengaruhi kredibilitas pelanggan terhadap bengkel. Maka dari itu, pihak bengkel memerlukan sebuah proses yang dapat meminimalisir kepuasan pelanggan setelah selesai perbaikan.
Hal ini dilakukan sebagai usaha untuk mendapatkan alternatif cara kerja yang baik, efektif, dan efisien. Bengkel mobil merupakan salah satu bisnis jasa yang melayani perbaikan mobil, Agar dapat bersaing di dunia usaha, maka bengkel harus memberikan perhatian yang lebih terhadap kualitas dan pelayanan kerja. Namun pada bengkel ini masih kurang dalam melakukan penataan dan penyimpanan pada bagian seperti peralatan mobil, body mobil yang berserakan di area tempat tersebut. Penataan pada barang dan peralatan ini sebenarnya sangat penting sebab masalah ini berpengaruh pada pencarian barang dan ketepatan waktu pelaksanaan kerja, serta menciptakan suasana nyaman dan hal ini sangatlah berpengaruh terhadap kinerja karyawannya. Penataan peralatan dan kurangnya ketelitian karyawan dalam membersihkan peralatan servis dapat menimbulkan ketidaknyamanan kerja pada rutinitas berikutnya seperti pada: peralatan, fasilitas kerja, tempat, dan lain-lain. Apabila peralatan berserakan dan tidak rapi, maka waktu pencarian barang dan peralatan khususnya suku cadang menjadi relatif lama, oleh karena itu, dilakukan penelitian mengenai penerapan 5S dengan tujuan memberikan usulan perbaikan 5S dan memberikan usulan SOP (Standard Operation Procedure) penerapan 5S untuk program perbaikan secara berkala.
2. Metode
5S adalah suatu metode penataan dan pemeliharaan wilayah kerja secara intensif yang berasal dari Jepang yang digunakan oleh manajemen dalam usaha memelihara ketertiban, efisiensi, dan disiplin di lokasi kerja sekaligus meningkatan kinerja perusahaan secara menyeluruh. Penerapan 5S umumnya diberlakukan bersamaan dengan penerapan kaizen agar dapat mendorong efektivitas pelaksanaan 5S. Di Indonesia metode ini dikenal dengan istilah 5R, sedangkan di Amerika dan Eropa dikenal dengan 5C.
Gambar 1. Konsep Serta Manfaat Penerapan 5S Di Perusahaan
Isi dari 5S antara lain :
1. 整理 (seiri), Ringkas, merupakan kegiatan menyingkirkan barang-barang yang tidak diperlukan sehingga segala barang yang ada di lokasi kerja hanya barang yang benar-benar dibutuhkan dalam aktivitas kerja.
2. 整頓 (seiton), Rapi, segala sesuatu harus diletakkan sesuai posisi yang ditetapkan sehingga siap digunakan pada saat diperlukan.
3. 清楚 (seiso), Resik, merupakan kegiatan membersihkan peralatan dan daerah kerja sehingga segala peralatan kerja tetap terjaga dalam kondisi yang baik.
4. 清潔 (seiketsu), Rawat, merupakan kegiatan menjaga kebersihan pribadi sekaligus mematuhi ketiga tahap sebelumnya.
5. 躾け (shitsuke), Rajin, yaitu pemeliharaan kedisiplinan pribadi masing-masing pekerja dalam menjalankan seluruh tahap 5S.
Penerapan 5S harus dilaksanakan secara bertahap sesuai urutannya. Jika tahap pertama (seiri) tidak dilakukan dengan baik, maka tahap berikutnya pun tidak akan dapat dijalankan secara maksimal, dan seterusnya. Konsep 5 S pada dasarnya merupakan proses perubahan sikap dengan menerapkan penataan, kebersihan dan kedisiplinan di temapat kerja. Dengan menerapkan prinsip ” A place for everything, and everything in its place, maka setiap anggota organisasi dibiasakan bekerja dalam lingkungan kerja dengan standar tempat yang jelas (Hirano, 1992:9).
Konsep 5 S yang merupakan bagian dari konsep kaizen(改善), memiliki arti penyempurnaan yang berkesinambungan baik dalam kehidupan pribadi, dalam keluarga, lingkungan sosial maupun di tempat kerja (Imai, 1992:VIII). Konsep 5 S merupakan budaya tentang bagaimana seoseorang memperlakukan tempat kerjanya secara benar. Bila tempat kerja tertata rapi, bersih, tertib maka kemudahan bekerja perorangan dapat diciptakan. Dengan kemudahan bekerja ini, empat bidang sasaran pokok industri yang meliputi: ƒ
- Efisiensi Kerja
- Produktifitas Kerja ƒ
- Kualitas Kerja, dan ƒ
- Keselamatan Kerja dapat lebih mudah dipenuhi.
Pemenuhan bidang sasaran pokok ini merupakan syarat bagi industri dalam bertumbuh kembang secara wajar. Manfaatnya jelas, bukan saja bagi perusahaan, namun juga bagi karyawan (Kristianto,1995:4).
Sebelum kegiatan 5 S dimulai hal yang pertama harus dilakukan adalah mengambil foto di sekeliling tempat kerja. Hal ini akan sangat berguna sebagai perbandingan bilamana 5 S dilaksanakan sepenuhnya (Hirano, 1992:12).
Sedangkan menurut 5 S dalam Softech (2007) 5 S ialah : 5 S adalah kepanjangan dari, Seiri, Seition, Seiso, Seiketsu, Shitsuke adalah pelatihan. Hal ini menjadi satu istilah, tetapi biasanya pengertiannya menjadi bias dalam kehidupan sehari- hari. Demikian juga dengan pemahaman artinya.
Seiri ialah proses memilah terhadap barang-barang yang diperlukan dengan yang tidak diperlukan, Sedangkan kegiatan seiton ialah kegiatan yang membuat langsung dapat menggunakan barang atau alat yang diperlukan karena barang dan alat tersebut sudah tersusun dengan baik. Sedangkan seiketsu ialah kegiatan untuk menjaga 3 S yaitu seiri, seiton, seiso. Shitsuke ialah kedisiplinan untuk mematuhi aturan 5 S, dan merupakan fondasi yang sangat penting dalam manajemen perusahaan. Bila 5 S dilaksanakan maka efisiensi produksi akan meningkat, serta berguna untuk terhindar dari kecelakaan. Berikut ini adalah penjelasan yang lebih detil mengenai bagian-bagian dari 5 S.
2.1 Konsep Seiri
Seiri yaitu memisahkan benda yang diperlukan dengan yang tidak diperlukan, kemudian menyingkirkan yang tidak diperlukan (ringkas). Sesungguhnya, terdapat banyak barang yang tidak diperlukan di dalam setiap pabrik. Barang yang tidak diperlukan artinya barang tersebut tidak dibutuhkan untuk kegiatan produksi saat ini (Hirano, 1992:13).
Langkah-langkah Melaksanakan Seiri
Untuk mengetahui barang-barang yang perlu dibuang, barang harus dipisahkan menjadi yang diperlukan dan yang tak diperlukan. Hal ini disebut dengan “Seiri visual” yang kemudian dilaksanakan menggunakan label merah seperti di perusahaan Toyota.
2.2 Konsep Seiton
Seiton yaitu menyusun dengan rapih dan mengenali benda untuk mempermudah penggunaan. Kata Jepang “seiton” secara harafiah berarti menyusun benda dengan cara yang menarik (rapi). Dalam konteks 5S, ini berarti mengatur barang-barang sehingga setiap orang dapat menemukannya dengan cepat. Untuk mencapai langkah ini, pelat penunjuk digunakan untuk menetapkan nama tiap barang dan tempat penyimpanannya (Yasuhiro,1995:249).
Langkah-langkah menerapkan Seiton
Setelah proses penyingkiran dengan label merah, tinggal barang yang diperlukansaja yang ada. Langkah berikutnya adalah memperlihatkan dengan jelas dimana posisi, apa barangnya, dan ada berapa banyak bahan sehingga barang-barang itu dapat dengan mudah diketahui. Seiton Visual memungkinkan pekerja dengan mudah mengenali dan mengambil kembali perkakas dan bahan, dan dengan mudah mengembalikannya ke lokasi di dekat tempat penggunaan. Pelat penunjuk digunakan untuk memudahkan penempatan dan pengambilan kembali bahan yang diperlukan.
Berikut adalah langkah-langkah pelaksanaan seiton atau penataan:
a. Langkah 1. Penempatan barang. Prinsip yang melandasi penentuan lokasi untuk tiap barang ialah menentukan barang yang sering digunakan dan
kemudian menempatkannya di sekitar pekerja yang menggunakannya. Barang lain yang jarang digunakan ditempatkan lebih jauh. Disamping itu,
barang harus diletakkan pada ketinggian antara pundak dan pinggang pekerja. Metode ini mengurangi waktu dan energi yang digunakan untuk
berjalan dari dan ke tempat penyimpanan.
b. Langkah 2. Menyimpan peti kemas. Setelah memutuskan mengenai ruang, peti kemas, misalnya kotak, lemari, rak, palet dan lain-lain, harus
dipersiapkan. Tetapi pembelian peti kemas yang baru harus benar-benar dihindari karena sasaran terakhir adalah mengurangi ruang serta
maminimalkan ukuran dan jumlah sediaan.
c. Langkah 3. Menunjukkan posisi untuk tiap barang. Pelat penunjuk yang berisi kode tempat dibuat dan digantungakan di plafon. Kode tempat adalah
alamat tempat dan alamat letak. Selain pelat penunjuk ini, pelat letak yang lebih khusus ditempatkan pada tiap rak. Contoh pelat tempat, pelat
letak, pelat kode barang, dapat dilihat pada gambar 2, seperti di bawah ini.
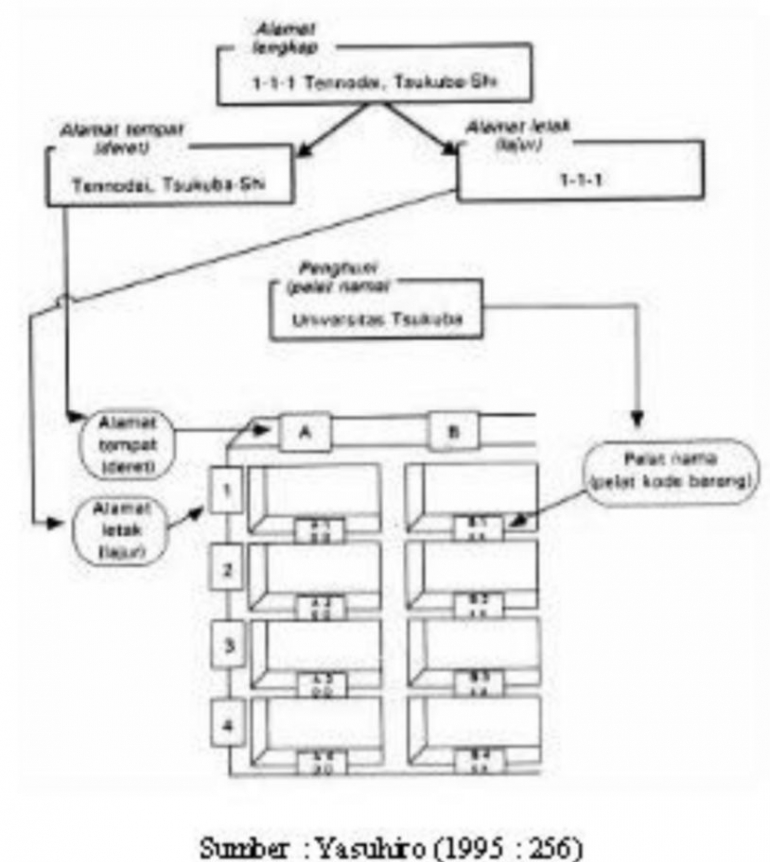
d. Langkah 4. Menunjukkan kode barang dan jumlahnya. Kode barang dan jumlahnya tertera pada barang itu sendiri melalui label kode barang dan
melalui pelat kode barang pada rak yang ditempati barang itu. Penggunaan pelat kode barang ini mirip dengan sistem untuk menentukan ruang
parkir. Dalam contoh ini, pelat nomor tiap mobil sesuai dengan label kode barang. Pelat kode barang sesuai dengan yang ditempatkan pada ujung
tiap tempat parkir yang menunjukkan nomor pelat dan nama pemilik. Contoh pelat kode barang dan label kode barang di tempat parkir dapat dilihat
pada gambar 3 seperti di bawah ini.
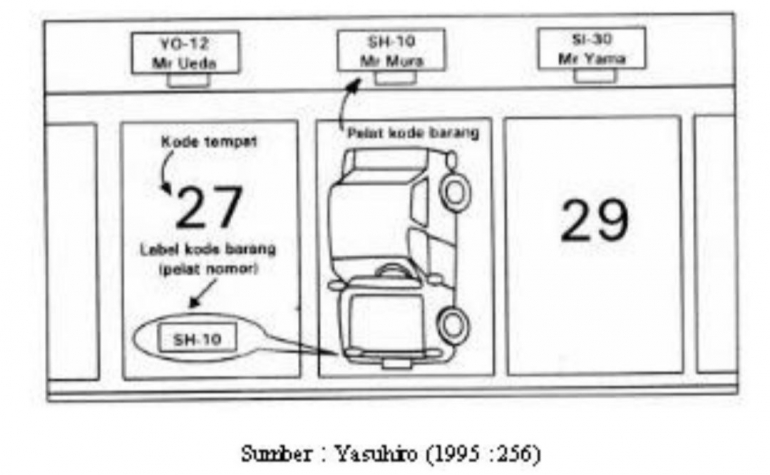
Untuk penunjuk jumlah maksimum atau ukuran lot dan jumlah minimum atau titik pesan ulang dari berbagai bahan harus ditentukan. Untuk menunjukkan jumlah sebagai ganti angka-angka, lebih baik jumlah yang dikehendaki dinyatakan secara visual dengan menggambar garis berwarna mencolok pada posisi yang tepat. Ini akan memungkinkan operator mengetahui tingkat jumlah minimum dan maksimum dengan sekejap tanpa harus membaca setiap jumlah yang ditulis. Contoh penunjuk jumlah sediaan maksimal dan minimal dapat dilihat pada gambar 4 seperti di bawah ini.
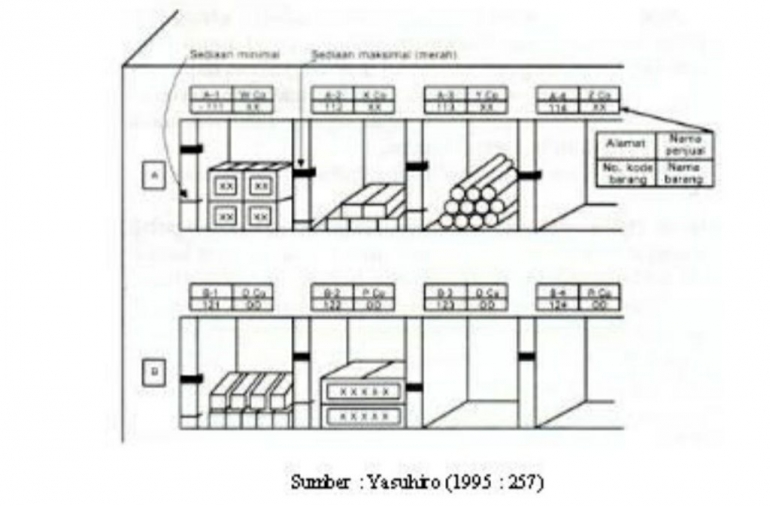
e. Langkah 5. Menjadikan Seiton suatu kebiasaan. Untuk menjaga tata tertib dalam pabrik, Seiri dan Seiton harus dilaksanakan secukupnya. Tindakan
itu adalah antara lain pemisahan bahan secara visual antara yang diperlukan dengan yang tidak, pengaturan bahan yang sering digunakan di dekat tempat penggunaannya, dan penggunaan pelat kode tempat, pelat kode barang, dan garis-garis penunjuk jumlah (Yasuhiro, 1995:255).
2.3 Konsep Seiso
Seiso yaitu selalu membersihkan, menjaga kerapihan dan kebersihan (resik). Iniadalah proses pembersihan dasar dimana suatu derah disapu dan kemudian dipel dengan kain pel. Karena lantai, jendela, maupun dinding harus dibersihkan, seiso di sini setara dengan aktifitas pembersihan berskala besar yang dilakukan setiap akhir tahun di rumah tangga Jepang. Meskipun pembersihan besar-besaran di seluruh perusahaan dilakukan beberapa kali dalam setahun, tiap tempat kerja perlu dibersihkan setiap hari. Aktifitas itu cenderung mengurangi kerusakan mesin akibat tumpahan minyak, abu, dan sampah. Contohnya, kalau ada pekerja yang mengeluh ada mesin yang rusak ini tidak berarti mesin itu perlu penyetelan. Sebenarnya, yang diperlukan mungkin hanya program pembersihan di tempat kerja (Yasuhiro,1995:249).
Untuk melaksanakan seiso atau resik, terlebih dahulu tentukanlah langkah-langkahnya sebagai berikut:
1. Tentukan apa yang hendak dibersihkan.
2. Tentukan siapa bertanggung jawab untuk setiap tugas Resik
3. Tentukan metode Resik.
4. Siapkan peralatan kebersihan
5. Pelaksanaan Resik (Hiroyuki, 1992:45).
Menentukan prosedur Resik dan Pemeriksaan Pokok permasalahan yang jelas
1. Yang pertama harus dilakukan adalah melihat keadaan sebenarnya di tempat kerja untuk mengetahui berapa banyak kotoran yang ada, apakah ada
kebocoran, kerusakan, dan lain-lain.
2. Hanya setelah itu dapat dibuat suatu daftar masalah dan pertimbangkan tindakan apa yang dapat diambil.
2.4 Konsep Seiketsu
Seiketsu yaitu terus menerus mempertahankan 3 S tersebut diatas, yakni Seiri, Seiton, dan Seiso. Seiketsu atau rawat, pada prinsipnya mengusahakan agar tempat kerja yang sudah menjadi baik dapat selalu terpelihara. Di tempat kerja yang rawat, kerawanan dan penyimpangan dapat segera dikenali, sehingga berbagai masalah dapat dicegah sedini mungkin (Kristianto, 1995:47).
Memelihara tempat kerja tetap bersih tanpa sampah atau tetesan minyak adalah aktivitas seiketsu. Antara seiso dengan seiketsu sangat berkaitan erat. Seiketsu atau pemeliharaan kerapihan secara terus menerus dalam pabrik, bergantung kepada Seiso yang membakukan kegiatan pembersihan sehingga tindakan ini spesifik dan mudah dikerjakan (Yasuhiro, 1995:265).
Adapun standar untuk membuang barang yang tak diperlukan adalah sebagai berikut:
1. Jangan sampai anda terbebani oleh berbagai barang di tempat kerja.
2. Sebaliknya tentukan standar untuk membuang barang-barang yang tidak diperlukan dari lingkungan anda.
2.5 Konsep Shitsuke
Shitsuke yaitu metode yang digunakan untuk memotivasi pekerja agar terus menerus melakukan dan ikut serta dalam kegiatan perawatan dan aktivitas perbaikan serta membuat pekerja terbiasa mentaati aturan (rajin). Hal ini dianggap sebagai komponen yang paling sukar dari 5S. Untuk aktivitas ini, pekerja Jepang diharapkan melatih pengandalian diri sendiri, bukan dikendalikan manajemen (Yasuhiro, 1995:266).
Shitsuke atau rajin berkaitan dengan kebiasaan karyawan yang harus dibina agar dapat menjaga dan meningkatkan apa yang sudah baik. Seperti, budaya antri, bersih, tepat waktu, tepat janji dan sebagainya harus dibina (Kristianto, 1995:61). Orang yang dapat memberikan kritik membangun dengan baik akan dapat melaksanakannya juga, karena mereka mempunyai komitmen terhadap:
1. Tempat Kerja Mereka memiliki komitmen terhadap pekerjaan mereka.
2. Produk Mereka memiliki komitmen untuk mempertahankan mutu produk yang dihasilkan oleh perusahaan.
3. Pelatihan Mereka memiliki komitmen untuk melatih bawahan mereka.
Berikut ini adalah tiga aspek penting dalam penerapan konsep shitsuke
1. Sanksi Sanksi diberikan kepada seluruh anggota perusahaan, jika melanggar atau tidak mematuhi peraturan yang terdapat di dalam 5 S.
2. PDCA (plan, do, check, action)
Langkah pertama dari kaizen adalah menerapkan siklus PDCA (plan, do, check, action) sebagian sarana yang menjamin terlaksananya |
kesinambungan dari kaizen guna mewujudkan kebijakan untuk memelihara dan memperbaiki atau meningkatkan standar. Siklus ini merupakan
konsep yang terpenting dari proses kaizen (Imai, 1998 : 4). Rencana (plan) berkaitan dengan penetapan target untuk perbaikan , karena kaizen
adalah cara hidup, maka harus selalu ada perbaikan untuk semua bidang, dan perumusan rencana guna mencapai target tersebut. Periksa (check)
merujuk pada penetapan apakah penerapan tersebut berada pada jalur yang sesuai rencana dan memantau kemajuan perbaikan yang direncanakan.
Tindak (action) berkaitan dengan standarisasi prosedur baru guna menghindari terjadinya kembali masalah yang sama atau menetapkan sasaran
baru bagi perbaikan berikutnya (Imai, 1998 : 5).
3. Penghargaan Penghargaan diberikan anggota perusahaan yang paling baik menerapkan 5S pada kegiatan produksi sehari-hari.
2.6 Produktivitas
Produktivitas adalah perbandingan antara total output barang dibagi dengan input yang meliputi sumber daya seperti tenaga kerja dan modal (Haizer, et al, 2014). Usaha peningkatan produktivitas menjadi perhatian dari para manajer atau pimpinan organisasi, meskipun demikian pada dasarnya para manajer atau para pimpinan organisasi itu hanya merupakan penanggung jawab dan pelaksanaan usaha peningkatan produktivitas. Gagasan dan kebijakan serta tanggung jawab akhir sebenarnya adalah terletak pada pimpinan puncak suatu organisasi. Faktor-faktor penentu keberhasilan peningkatan produktivitas menurut Siagian, (2014) yaitu diantaranya:
1) Perbaikan terus menerus yaitu upaya meningkatkan produktivitas kerja salah satu implementasinya ialah bahwa seluruh komponen harus
melakukan perbaikan secara terus-menerus.
2) Peningkatan mutu hasil pekerjaan yang dilaksanakan oleh semua komponen dalam organisasi.
3) Pemberdayaan sumber daya manusia.
4) Filsafat organisasi yang sesungguhnya titik tolak perumusan etos kerja bersifat filsafat yang pada mulanya mungkin dirumuskan oleh para pendiri
(founding father) organisasi yang bersangkutan.
2.7 Diagram Sebab Akibat (Fishbone Diagram)
Heizer dkk. (2017) menyatakan bahwa diagram ini disebut juga diagram tulang ikan (Fishbone Chart) dan berguna untuk memperlihatkan faktor-faktor utama yang berpengaruh pada kualitas dan mempunyai akibat pada masalah yang kita pelajari, selain itu kita juga dapat melihat faktor-faktor yang lebih terperinci yang berpengaruh dan mempunyai akibat pada faktor utama tersebut yang dapat kita lihat pada panah-panah yang berbentuk tulang ikan pada diagram fishbone tersebut. Prinsip yang digunakan untuk membuat diagram sebab akibat ini adalah sumbang saran atau brainstorming. Faktor-faktor penyebab utama dalam diagram sebab akibat ini dapat dikelompokkan dalam:
1). Material (bahan baku)
2). Machine (mesin)
3). Man (tenaga kerja)
4). Method (metode)
5). Environment (lingkungan).
Contoh dari diagram fishbone dapat dilihat dalam Gambar 5.
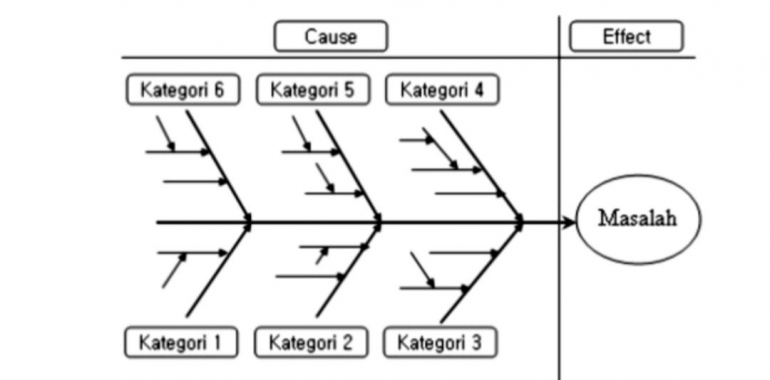
3. Hasil dan Pembahasan
Saat Bengkel Body Repair menerima order dari customer. Pihak Bengkel Body Repair akan menanyakan serta memeriksa kendala pada mobil tersebut agar bisa melakukan tindakan perbaikan. Setelah mengetahui kendala dari mobil milik customer tersebt maka pihak benggel baru akan melakukan perbaikan atas persetujuan customer. Proses-proses yang dilakukan pada bengkkel ini adalah melakukan perbaikan, dempul, pengecatan, dan poles atau finishing mobil.
3.1 Analisis Diagram Fishbone
Gambar 6. Diagram Fishbone
Dari Gambar 6 Diagram Fishbone dapat dianalisis dari tiap-tiap tulang ikan atau penyebab terjadinya menurunya produktivitas. Setelah dilakukan analisis dengan diagram Fishbone maka dapat diketahui kemungkinan-kemungkinan yang menyebabkan pekerjaan menjadi lama untuk proses perbaikan. Untuk mesin, material, manusia dan lingkungan terjadi karena faktor manusia/karyawan dalam bekerja. Untuk metode tidak adanya penggunaan metode yang terukur dan berkesinambungan karena tidak efisien pada waktu dan biaya disebabkan karena tools yang sulit dicari/berantakan sehingga harus dibuat tempat tools untuk memudahkan mengambil dan mencari tools yang ingin digunakan tanpa membutuhkan waktu lama saat mencari. Permasalahan yang paling dominan adalah banyak menyangkut mengenai faktor manusia atau Tidak adanya standar kualitas SDM Produktivitas Rendah Lambatnya proses produksi Environment Methods Machines Karyawan kurang peduli terhadap area kerjanya Kurangnya pengetahuan budaya 5S Tidak adanya penelitian 5S Pencarian dan pengambilan peralatan yang sulit Ketidaknyamanan area kerja Ketidakefisienan waktu dan biaya Tidak menggunakan metode yang terukur dan berkesinambngan Sulit mencari tools karena berantakan Mesin off Mesin melakukan pergantian item Material Man Kebersihan lingkungan kerja yang tidak terjaga karyawan dan keamanan karyawan tersebut. Setelah diketahui penyebab yang paling dominan terhadap permasalahan, langkah selanjutnya yaitu menentukan rencana penanggulangan terhadap permasalahan di Bengkel Body Repair yang dapat dilihat pada tabel 1 berikut.
Tabel 1. Rencana Penanggulangan Rendahnya Produktivitas
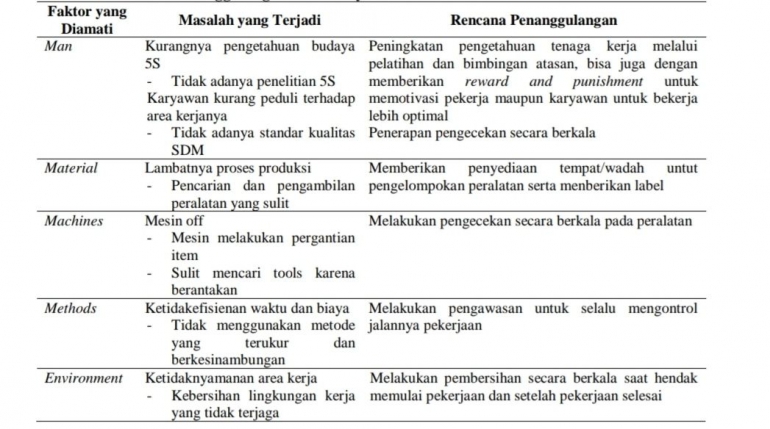
4.1 Kesimpulan
Bahwa untuk meningkatkan produktivitas di Bengkel Body Repair dapat dimulai dengan melakukan implementasi 5S sehingga dapat mengatasi masalah yang terjadi pada lingkungan kerja Perbaikan. Tindakan perbaikan yang meliputi 5S sebagai berikut:
Seiri : Dengan memilih barang yang diperlukan dan tidak diperlukan yang ada di Bengkel Body Repair.
Seiton : Mengatur alat kerja termasuk dokumen dan arsip yang digunakan dengan rapi dan sepenuhnya menghilangkan kegiatan pencarian
sehingga mereka dapat dengan mudah ditemukan dengan cepat tanpa menambah waktu proses. Seiso : menjaga kebersihan tempat kerja
dalam hal lantai, barang, bangunan dan alat yang ada di lingkungan kerja.
Seiketsu : Mempertahankan seiri, seiton, dan seiso dengan memberikan SOP dan peraturan yang jelas.
Shitsuke : Menerapkan kedisiplinan pada setiap karyawan Bengkel Body Repair dan melakukan inspeksi berkala yang dilakukan oleh kepala produksi.
4.2 Saran
Analisis yang dilakukan hanya untuk mendukung penerapan 5S diperusahaan tanpa membahas aspek-aspek lain yang terkait dengan penggunaan variabel lain. Maka untuk penelitian selanjutnya diharapkan membahas aspek-aspek lain yang terkait dengan kegunaan 5S tersebut untuk mengurangi waste yang terjadi di lingkungan kerja sehingga produktivitas kerja meningkat.
5. Daftar Pustaka
Amrun, A. (2008). Produktivitas dan Budaya Kerja. Retrieved Oktober Rabu, 2015 From
http://ahmadiamrun.multiply.com/jurnal/item/18/090106.html.
Farida, I. (2009). Budaya Organisasi dan Produktivitas Kerja. Jurnal Tapis, 5(10),103-120.
Hirano, Hiroyuki.1996. Penerapan 5S di Tempat Kerja : Pendekatan Langkah-langkah Praktis (Terjemahan). Jakarta : PQM Consultans.
Purba, H.H. (2008). Diagram Fishbone dari Ishikawa. Retrieved from http://hardipurba.com/2008/09/25/diagram-fishbone-dari-ishikawa.html diakses tanggal 29 mei 2020 (09.19 WIB).
Osada, Takashi. 2004. Sikap kerja 5S. Jakarta : PPM.
Osada, Takashi. 1995. Sikap Kerja 5S (Terjemahan). Jakarta : Pustaka Binaman Pressindo.
Sasongko, D. 2008. Diagram Sebab-Akibat (Fishbone Diagram). Djoko-Sasongko.blogspot.com. (13 Desember 2019).
Simanjuntak, P.J. 1983. Produktivitas Kerja : Pengertian Ruang dan Lingkupnya. Prisma No. 11. LP3ES. Jakarta.
Baca konten-konten menarik Kompasiana langsung dari smartphone kamu. Follow channel WhatsApp Kompasiana sekarang di sini: https://whatsapp.com/channel/0029VaYjYaL4Spk7WflFYJ2H