Siapa sangka, ternyata Pabrik Toyota yang mendunia itu, dulunya adalah Pabrik Tenun. Bagaimana ceritanya?
Adalah tiga orang penting yang menciptakan sejarah TOYOTA PRODUCTION SYSTEM (TPS). Ketiganya adalah Sakichi Toyoda (1867 – 1930, seorang industrialis Jepang), Kiichiro Toyoda (1854 – 1952, dan merupakan putra dari Sakichi Toyoda), dan Taiichi Ohno (1912 – 1990) yang merupakan seorang Production Engineer dan Businessman.
TPS bermula dari temuan Sakichi Toyoda terhadap mesin tenun miliknya. Sederhana temuannya. Yaitu, ketika terjadi suatu masalah pada mesin tenun, dampaknya akan selalu mengakibatkan produk gagal atau No Good Product/Reject Product.
Dihantui produk gagal, membuat Sakichi Toyoda berpikir keras untuk menghindarinya. Caranya? Jitu!
Ia memasang sensor otomatis pada mesin tenunnya. Dengan begitu, ketika terjadi proses produksi yang tidak normal, abnormality, maka mesin tenun akan berhenti secara otomatis. Hasilnya? Jelas luar biasa! Karena, tidak ada lagi produk gagal. Ya, bagaimana mau gagal, lantaran setiap terjadi abnormality, mesin tenun akan terhenti. Mesin tenun akan kembali dioperasikan, setelah keadaan tidak normal seperti misalnya benang putus, benang kusut, bandul jatuh, berhasil diperbaiki.
Temuan Sakichi Toyoda yang pada 1902 melakukan otonomisasi mesin atau proses produksi yang berhenti bila terjadi abnormality inilah yang dinamakan konsep JIDOKA.
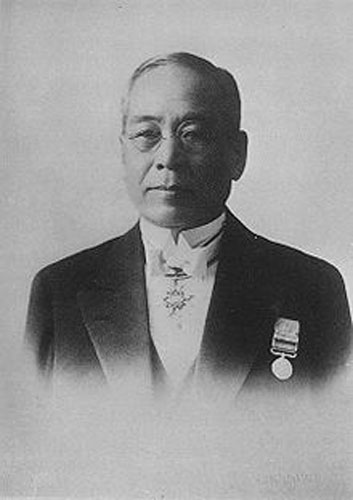
Secara lengkap, JIDOKA dalam TPS adalah suatu alat atau sistem yang dipergunakan untuk mengetahui atau mendeteksi ketidaknormalan (abnormality) proses. Sistem atau alat ini kemudian diberi wewenang untuk menghentikan proses produksi dengan alasan adanya ketidakberesan. Contoh, pada lini produksi yang menggunakan conveyor, operator dianjurkan untuk menarik tuas ‘line stop’ untuk menghentikan produksi, hingga leader datang mengecek dan mengurai abnormality menjadi normal kembali.
Sebagai industrialis yang nasionalis dan visioner, Sakichi Toyoda tidak memaksakan namanya ditabalkan sebagai brand produk otomotifnya. Ia justru legowo mengubah TOYODA menjadi TOYOTA. Keputusan ini ternyata menjadi strategi pemasaran yang hebring. Betapa tidak? Publik, ternyata lebih mudah menyebut Toyota ketimbang Toyoda. Nilai lebih lainnya, penulisan dalam aksara Jepang juga jadi mudah karena menghilangkan tanda apostrop (“), yang mirip tanda kutip. Itu artinya, membuat proses pencetakan huruf bertuliskan Toyota---baik di kendaraan, aksesoris, maupun komponen---dalam aksara Jepang menjadi lebih simple.
Lantas, bagaimana sumbangsih Kiichiro Toyoda? Ternyata, sama luar biasanya dengan sang ayah.
Pada 1930, ketika Toyota Group baru meninggalkan industri tenun dan berfokus ke bisnis otomotif, sang ayah, Sakichi Toyoda, mengutus Kiichiro Toyoda ke Amerika Serikat. Tujuannya tak lain untuk mempelajari seluk-beluk produksi dan bisnis perusahaan otomotif milik Henry Ford (1863 – 1947). Kala itu, perusahaan sang juragan merupakan perusahaan otomotif terbesar dengan meluncurkan mobil bermerek, Ford.
Taat pada sang ayah, Kiichiro menekuni pembelajarannya di Negeri Paman Sam.
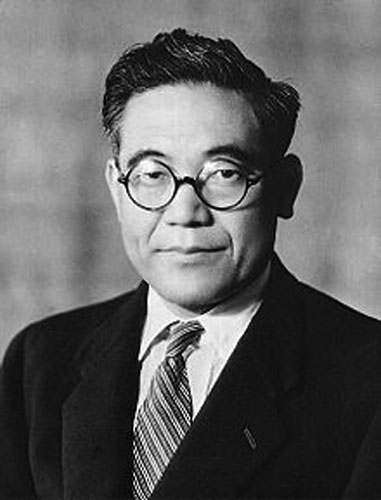
Nah, ketika kembali ke tanah kelahirannya, Jepang, Kiichiro memboyong dan mempraktikkan sistem conveyor, yakni sistem produksi yang dilakukan di atas roda berjalan. Tak pelak, adaptasi (proses produksi) dari Ford ini merupakan sebuah konsep yang sangat kuat dan tepat, guna mengembangkan kondisi pasar otomotif di negerinya saat itu.
Kiichiro juga mematangkan konsep yang memungkinkan proses produksi berlangsung sesuai dengan kebutuhan dari proses berikutnya. Artinya, proses produksi dilakukan, sebanyak yang dibutuhkan dan dibuat dalam waktu yang juga telah ditetapkan. Dengan begitu, yang namanya produksi dan pergerakan material diatur sedemikian cermat, kontinyu dan sinkron dalam sebuah rangkaian atau alur proses. Inilah yang dikembangkan Kiichiro menjadi salah satu keunggulan TPS, dan diberi sebutan sistem JUST IN TIME. Di ‘tangan dingin’ Taiichi Ohno, sistem Just In Time pun akhirnya mengalami penyempurnaan, selain menerapkan sistem KANBAN.untuk meningkatkan level produksi.
Kini, meski sudah lebih dari dua abad, sistem produksi yang dikembangkan oleh para the founding fathers Toyota, masih dipertahankan.
Dan, saya beruntung, dapat menyaksikan filosofi bisnis tersebut menyemai abadi. Saya memantau langsung bagaimana hal-hal yang mengakar itu tetap bertahan bahkan menjadi acuan kerja di Pabrik Toyota Sunter 1, Jakarta Utara, pada Rabu, 10 Juni 2015. Kesempatan emas ini terlaksana dalam traveling bertajuk Kompasiana Visit PT Toyota Motor Manufacturing Indonesia (TMMIN).
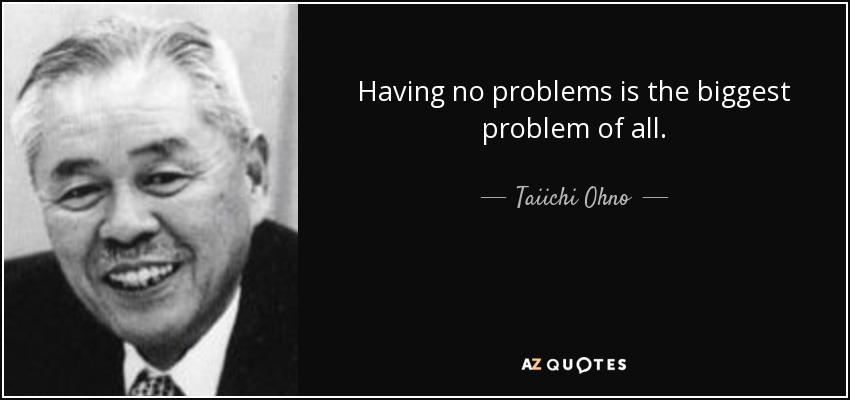
Sila baca reportase kunjungan tersebut, pada tulisan sebelumnya: Menimba Ilmu ‘Monozukuri’, Melihat Langsung ‘Toyota Way’.
* * * * *
Sebelum memasuki pabrik engine, masing-masing anggota rombongan Kompasianer dibekali radio receiver berukuran mini, lengkap dengan earphone-nya. Fungsinya satu arah, karena hanya untuk memudahkan menangkap pembicaraan pemandu, selama berada di dalam area pabrik yang (memang) cukup bising.
Keren ya, jadi pemandu factory tour enggak usah ngomong sambil teriak. Sementara kami sebagai peserta juga nyaman menyimak penjelasan melalui earphone sebelah telinga, meski di tengah suasana rada berisik.
Memasuki area pabrik, rombongan dipandu Rosid, staf TMMIN yang mengetahui secara mendalam serba-serbi proses produksi. Pria bertubuh subur dan mengenakan seragam berwarna abu-abu muda ini lebih dulu menjelaskan tentang Toyota Indonesia – History of Manufacturing Products.
“Dari tahun 1985 hingga 2004, pabrik kita sudah memproduksi 13 tipe mesin. Mulai dari tipe 5K untuk Toyota Starlet, 7K untuk Kijang Kapsul, 4A untuk Corolla, 3S untuk Corona, 14D untuk Truk Dyna, 1Z, NZ dan AZ. Sedangkan sejak tahun 2005, kita hanya memproduksi mesin 1 TR dan 2 TR,” tutur Rosid sembari memperlihatkan sejumlah replika mesin tersebut.
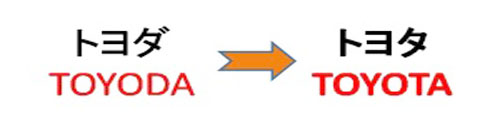
Selama proses produksi berlangsung, Rosid mengatakan, penerapan efisiensi waktu kerja menjadi salah satu yang menjadi perhatian Korporat. “Ini kaitannya dengan man power. Prinsip yang dijalankan adalah bagaimana setiap orang dapat menghargai waktu. Meskipun, hanya mampu mengurangi durasi proses kerja selama satu detik. Tapi, apabila yang cuma satu detik itu bisa di-reduce, maka bila ada berdetik-detik lagi, hasilnya akan menjadi banyak juga waktu kerja (dalam proses produksi) ini yang dapat diefisienkan,” tuturnya.
Efisiensi waktu menjadi salah satu yang sangat penting dalam TPS. Karena, Sistem Produksi Toyota memang senantiasa berusaha meningkatkan profit dengan cara mengeliminasi atau bahkan menghilangkan muda. Muda disini, kerapkali diartikan sebagai waste, pemborosan, dan sesuatu yang tidak memberikan nilai tambah (added value).
Sederhananya begini:
Gerak seorang operator dalam proses produksi, senantiasa terdiri dari Kerja (work) dan Muda (waste). Kerja itu sendiri, terdiri dari gerakan yang menghasilkan nilai tambah, sekaligus gerakan yang tidak menghasilkan nilai tambah.
Ambil contoh, seperti dimuat situs sistemproduksitoyota.com, adalah gerakan memasang tutup ke pulpen. Urutannya, sebagai berikut:
- * Tangan menjangkau pulpen dan tutupnya. (1 detik) … [Tak Punya Nilai Tambah]
- * Tangan mengambil pulpen dan tutupnya. (1 detik) … [Tak Punya Nilai Tambah]
- * Tangan mengarahkan pulpen dan tutupnya. (1 detik) … [Tak Punya Nilai Tambah]
- * Tangan memasang tutup pulpen. (1 detik) … [Punya Nilai Tambah]
- * Tangan meletakkan kembali pulpen. (1 detik) … [Tak Punya Nilai Tambah]
Dari lima kerja yang dilakukan tangan, hanya ada satu proses yang memiliki nilai tambah, yaitu proses nomor 4. Nah, bagaimana mengeliminasi waste adalah berarti bagaimana me-reduce proses urutan kerja dari tangan pada nomor 1, 2, 3, dan 5.
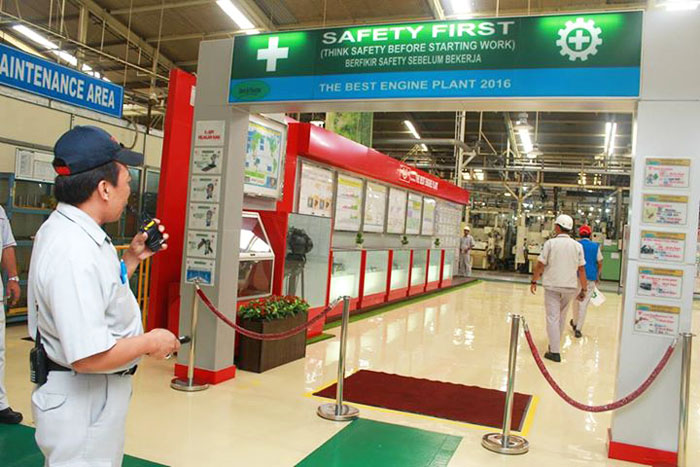
Mengapa ini penting? Sekali lagi, lihat apabila ini dituangkan dalam prosentase. Dari 5 pekerjaan, hanya ada 1 yang memiliki nilai tambah. Maka, perbandingan antara [Pekerjaan yang Punya Nilai Tambah] vs [Pekerjaan yang Tak Punya Nilai Tambah] adalah: 1/5, atau mencapai 20 persen!
Sungguh, angka seperlima, atau 20 persen ini, akan menjadi sangat berarti dan semakin banyak, apabila dijumlahkan dengan proses produksi pada bagian-bagian kerja, atau pada line kerja lainnya. Terbayang ‘kan, betapa hebat TPS yang sejak dua abad silam, sudah memperhitungkan hal-hal yang saklek alias zakelijk seperti ini. Luar biasa!
Dari perkara menutup pulpen saja, kita bisa belajar, bahwa selalu terjadi, kondisi muda atau waste itu lebih banyak daripada kerja (work) itu sendiri. Inilah yang membuat TPS menerapkan filosofi KAIZEN, atau improvement.
Karakter huruf Kanji asli dari kata KAIZEN terdiri dari dua suku kata. KAI yang artinya ‘perubahan’ atau ‘kegiatan untuk memperbaiki’, dan ZEN yang berarti ‘kebaikan’ atau ‘tindakan yang bermanfaat’. Sehingga secara harfiah, KAIZEN bisa dimaknai dengan ‘untuk menjadi baik melalui perubahan’. Atau, sesuai arti improvement itu sendiri, yaitu perbaikan secara berkesinambungan.
Ketika semakin memasuki area pabrik, Rosid yang penuh sabar memandu rombongan Kompasianer menjelaskan tentang AGV atau Automated Guided Vehicle. Apa itu? Ya, inilah satu penciptaan teknologi---dalam rangka Kaizen---, yang berfungsi menggantikan tenaga atau pekerjaan manusia.
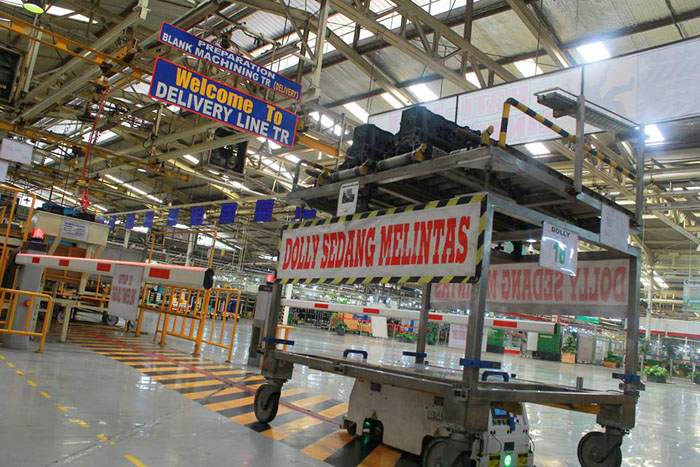
“AGV untuk mengganti tenaga orang, dulu pekerjaa ini memerlukan dorong dari member, atau operator. Padahal, kalau didorong akan mengakibatkan ergonomic yang tidak bagus bagi tubuh seseorang. AGV ini murni hasil pemikiran dan ide-ide cemerlang dari level bawah. Inilah bukti hasil positif Kaizen yang berlangsung di Toyota Way, dan dilaksanakan di Pabrik Toyota Sunter 1 ini,” ujar Rosid bangga.
Keunggulan Gunakan KANBAN
Ketika menyusuri Area Logistik, kepada rombongan, Rosid sempat menjelaskan tentang sistem KANBAN. Yaitu, semacam kartu informasi elektronis yang menjelaskan pergerakan barang. Kanban berfungsi sebagai sinyal produksi suatu barang, dan juga sinyal perintah untuk memindahkan barang dari satu pos produksi ke pos lain. Tak salah, kalau Kanban juga disebut sebagai alat kontrol untuk mewujudkan produksi yang tepat waktu, atau Just In Time.
Menurut Rosid, bisa dibayangkan betapa akan penuh sesaknya area pabrik dengan komponen produk yang dibuat, apabila tidak ada sistem Kanban. “Dalam hal ini, kami mempergunakan sistem Kanban (dari supplier, dan internal produksi). Sehingga, dengan pengaturan tersebut, space ruangan menjadi tidak terlalu besar, karena mempergunakan sistem Just In Time. Kalau tidak menggunakan Just In Time, bisa-bisa produk barang menumpuk sampai ke atap pabrik, dan dipenuhi dengan cylinder block.,” ujarnya sembari terkekeh.
Apalagi saat ini, tambah Rosid, Pabrik Toyota Sunter 1 mampu memproduksi cylinder block sekitar 800 unit per hari. Targetnya, dalam satu bulan mencapai antara 18.000 sampai 20.000 unit.
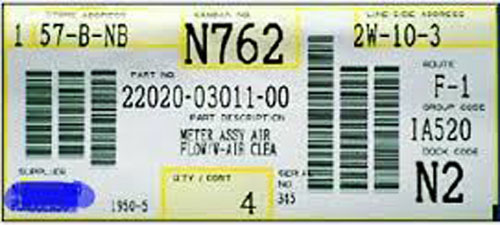
Bisa dibayangkan, dengan volume produksi sebanyak itu, dan dengan space area pabrik yang ada, menjadikan sistem Kanban sangat penting dalam memperlancar flow proses dan mengendalikan Inventory in Process.
Sejumlah aturan yang melingkupi sistem Kanban adalah: Memproduksi dan mensuplai barang hanya sesuai dengan jumlah kanban yang diterima; Part/barang harus bergerak bersama Kanban; Tidak memproduksi dan mensuplai tanpa Kanban; dan, Saat pertama part/barang diambil dari boks, Kanban harus diambil dan diletakkan ke pos Kanban.
Sedangkan manfaat pengaturan sistem produksi menggunakan Kanban, ada banyak sekali:
- Memberikan instruksi kerja kepada operator produksi.
- Memudahkan mengontrol kondisi lini produksi.
- Mengetahui kondisi sedini mungkin.
- Mencegah penumpukan barang.
- Secara tidak langsung mencegah kerusakan barang.
- Pengiriman barang sesuai waktu.
- Tepat dalam pengiriman.
- Kelancaran produksi, karena Kanban secara sistem adalah perintah untuk membuat dan mentransportasikan barang.
- Produksi lebih teratur.
- Lokasi kerja lebih teratur
Dengan menerapkan sistem Kanban pula, imbuh Rosid, kondisi di area pabrik menjadi semakin mudah terlihat perkembangannya, tidak saja dari sisi ‘5R’, kualitas, Standard Operation and Procedure (SOP), serta dari penegakan atas aturan-aturan yang berlaku.
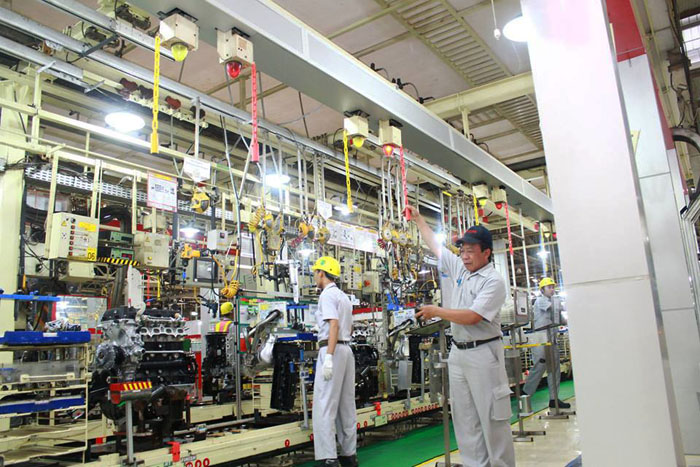
Rosid menyebutkan ‘5R’, apa itu?
Yup! Inilah pakem kerja dalam sistem produksi yang berlaku juga di Pabrik Toyota Sunter 1. Ada yang menyebut ‘5R’, tapi ada juga yang bilang ‘5S’. Lengkapnya, begini:
Pertama, SEIRI atau Ringkas. Merupakan kegiatan memisahkan barang atau material yang diperlukan dan tidak diperlukan, sekaligus menyingkirkan yang tidak diperlukan di area kerja. Dengan demikian, segala barang yang ada di lokasi kerja hanya barang yang benar-benar dibutuhkan dalam aktivitas kerja.
Kedua, SEITON alias Rapi. Bila tidak memenuhi unsur Seiton, maka saat proses produksi dimulai, operator dipastikan bingung mencari dimana letak barang yang diinginkan, sehingga operator harus lebih dulu mencari-cari. Bisa juga terjadi salah menggunakan jig, tool dan lainnya, karena tidak ada identifikasi atau pelabelan. Ekses buruk lainnya adalah pengontrolan area kerja menjadi lebih sulit akibat barang tidak kelihatan jelas.
Ketiga, SEISO atawa Resik. Artinya, mempertahankan kebersihan mesin, peralatan kerja dan tempat kerja dari segala kotoran. Sehingga, segala peralatan kerja tetap terjaga dalam kondisi yang baik. Sudah tentu, SEISO memiliki keuntungan, yaitu area kerja menjadi bersih, sehingga orang yang ada di area tersebut menjadi betah dan nyaman, dan, siapa saja terhindar dari kecelakaan akibat labtai licin oleh minyak pelumas dan sebagainya.
Keempat, SEIKETSU atau Rawat. Maknanya, kegiatan penerapan konsep kebersihan pada diri sendiri dan lingkungan, serta berkesinambungan melaksanakan ketiga langkah sebelumnya, SEIRI, SEITON dan SEISO.
Kelima, SHITSUKE atau Rajin, yaitu pemeliharaan kedisiplinan pribadi masing-masing pekerja dalam menjalankan seluruh tahap ‘5S atau 5R’ secara bertahap dan berurutan.
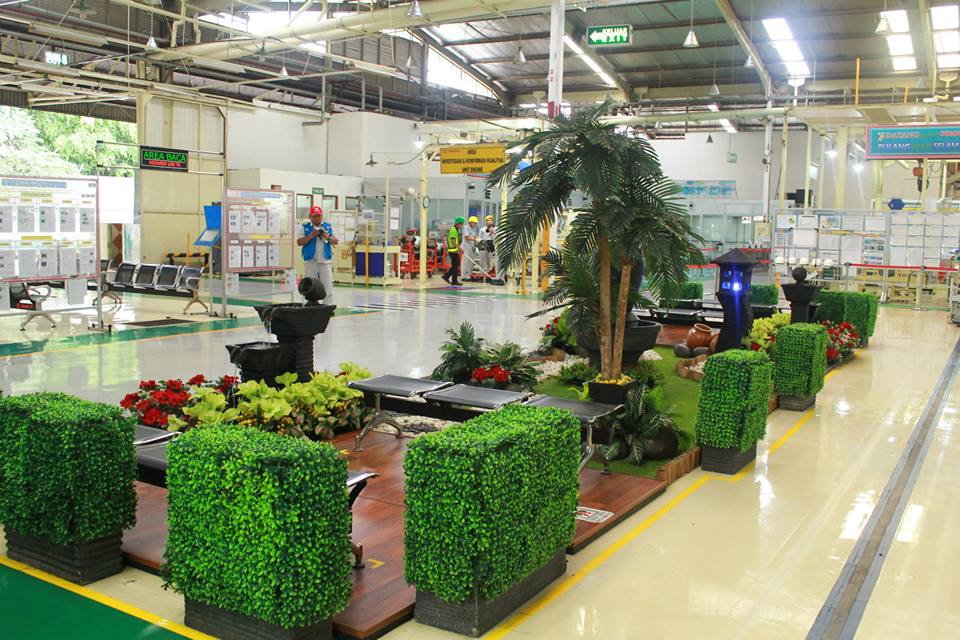
Keunggulan Sistem JUST IN TIME
Selain Kanban, yang juga banyak disebut-sebut Rosid, ketika memandu rombongan Kompasianer blusukan di pabrik, adalah Just In Time, yang berarti perusahaan/lini produksi/operator melakukan proses produksi barang hanya sebanyak jumlah yang diminta (konsumen) dan pada saat dibutuhkan. Dengan begitu, dapat mengurangi biaya pemeliharaan dan menekan kemungkinan kerusakan atau kerugian akibat stok, atau timbunan barang.
Inilah sistem yang dirintis Toyota Motor Corporation, dan dikenal sebagai TPS, untuk kemudian semakin moncer gaungnya dengan istilah Lean Production atau Lean Manufacturing.
Filosofi Just In Time, seperti dimuat sistemproduksitoyota.com, sangat sederhana. Yakni, penyimpanan persediaan/inventory yang tidak terpakai adalah pemborosan sumber daya. Nah, Just In Time melihat inventory sebagai sesuatu yang (dapat) memunculkan biaya tersembunyi. Makanya, dengan Just In Time, korporat dapat mendefinisikan level inventory sehingga mudah dipantau, dan semua ini berkaitan erat juga dengan performa manajemen secara keseluruhan.
* * * * *
Oh ya, agak mundur sedikit, ketika mulai memasuki area Pabrik Toyota Sunter 1, semboyan untuk memperhatikan masalah safety sangat menonjol. Ada semacam gerbang berwarna merah yang dilengkapi dengan tulisan: SAFETY FIRST. Think safety before starting work. Berpikir safety sebelum bekerja.
Masalah safety juga menjadi urutan pertama dari enam Key Performance Indicator (KPI) Achievement. Lima lainnya adalah, environment, quality, productivity, cost, dan human resources development (HRD).
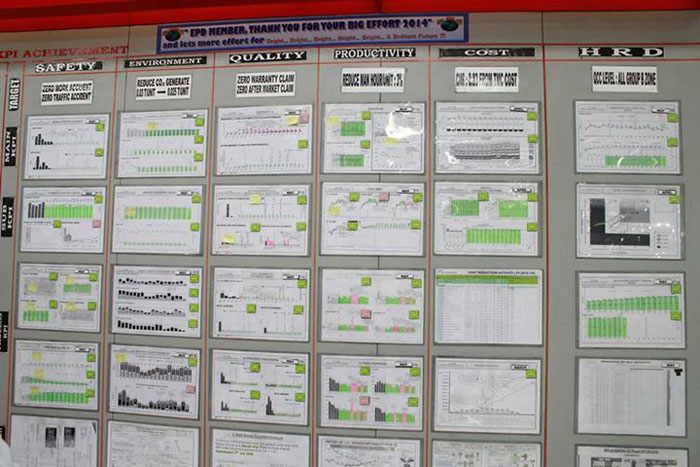
Untuk masalah safety ini, Rosid menjelaskan, TMMIN sangat serius melindungi keselamatan para pekerjanya. Termasuk, mereka yang menggunakan sepeda motor sebagi moda transportasi sehari-hari. Kiatnya?
“Setiap bulan sekali, kita melakukan patroli untuk mengecek kendaraan bermotor para karyawan. Patroli dilakukan pada jam 06.30 pagi, sebelum jam masuk kantor. Adapun yang bertugas melakukan patroli adalah para Supervisor sampai Division Head. Pengecekan yang dilakukan adalah menyangkut kelengkapan sepeda motor. Kami berharap, kendaraan bermotor yang dipergunakan oleh karyawan adalah tetap standar keluaran pabrikan. Itu artinya, modifikasi knalpot motor jenis racing yang menimbulkan suara bising akan dilarang penggunaannya. Begitu pula dengan lampu-lampu yang ada di motor, tidak boleh untuk dimodifikasi. Selain itu, kami juga sudah pasti mengecek SIM dan STNK pemilik kendaraan bermotor. Umumnya pelanggaran yang ditemui, biasanya adalah tentang lampu rem, dan spion yang dimodifikasi menjadi berukuran kecil,” urai Rosid membuat sebagian Kompasianer tertegun menyimak penjelasannya.
Urusan safety, menurut Rosid lagi, termasuk dalam salah satu material ‘rumus’ dalam Engine Production Division Activity. Rumus lengkapnya, begini: Safety (get to work) + CBC (foundation of our process) + Three Pilars Management (our daily worksite management) = Beki Daka Koujou (Volume Production Up).
Bagaimana dengan CBC?
Rosid menuturkan lugas. “Aktivitas yang berlangsung dalam pabrik assembling production menerapkan tiga pilar CBC, yaitu Clean, tidak ada yang namanya kabel berantakan di dalam line kerja; Bright, tidak mengenakan warna-warna hitam dan gelap lainnya; dan, Comfort, kerja yang nyaman. Dengan pilar CBC yang akhirnya membuat nyaman, maka proses produksi diharapkan dapat memenuhi target,” terangnya.
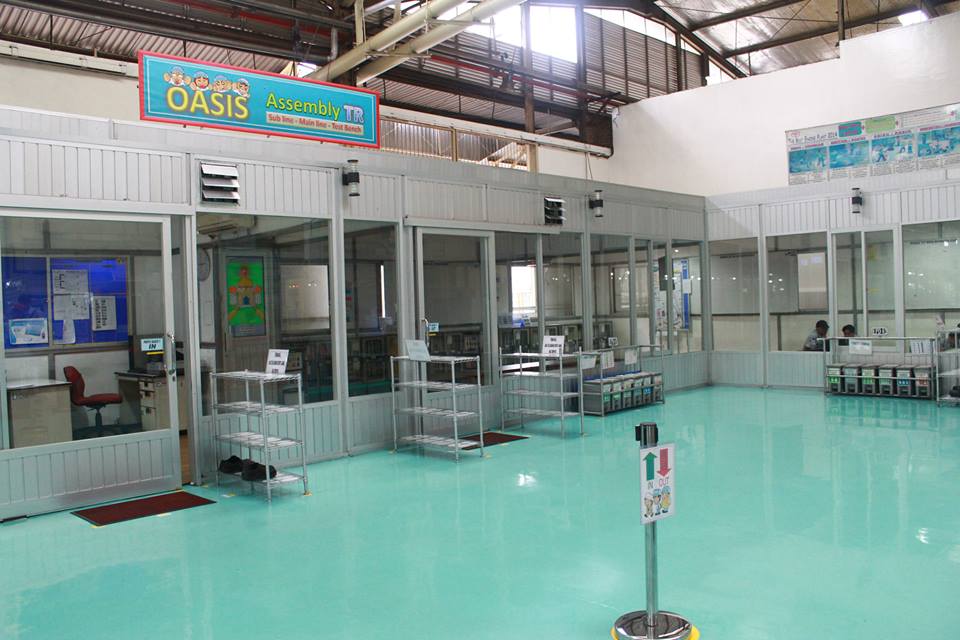
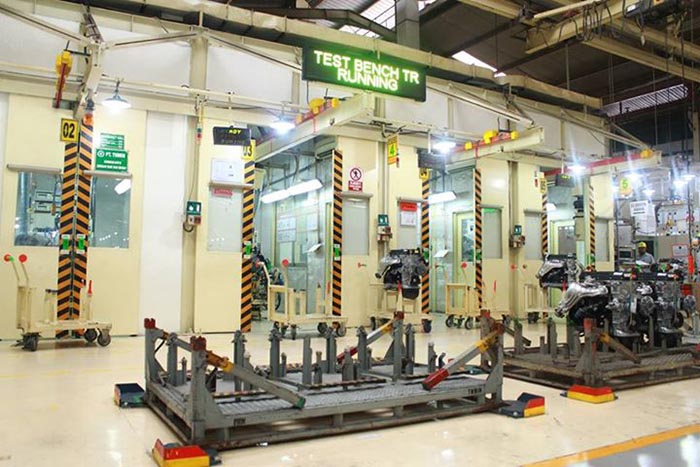
Diantara yang membuat nyaman para member atau operator di area pabrik ini adalah adanya ruang istirahat yang sangat comfortable, nyaman.
“Oasis, adalah ruangan istirahat untuk member. Dulu, kacanya memiliki jendela yang hanya dapat sedikit terbuka, sehingga ketika ada member yang beristirahat di dalam Oasis, tidak akan dapat diketahui yang bersangkutan sedang melakukan apa. Sekarang, jendelanya dihilangkan sama sekali, tinggal jendela yang transparan, sehingga dari luar pun dapat terlihat apa yang sedang dilakukan member ketika beristirahat di Oasis. Pokoknya, suasana di Oasis sangat nyaman,” tutur Rosid.
Sambil terus memandu rombongan mengelilingi pabrik, Rosid menjelaskan mengenai makna Three Pilars Management. “Intinya adalah, bagaimana mengatur irama kerja, bagaimana membuat man power pada bagian produksi dapat melakukan pekerjaan yang terbaik; dan bagaimana pihak manajemen dapat terus meningkatkan kualitas produksi,” jelasnya.
Ketika berada di area assembly land pabrik, Rosid memperlihatkan tanda penunjuk arah dan lokasi. Mirip seperti rambu-rambu lalu-lintas, tetapi berukuran lebih mini. “Tertera arah dan lokasi untuk memudahkan siapa saja yang berkunjung di sini menuju ke tempat yang akan dituju, misalnya ke Assembling Line (Dojo Room), Machining Cylinder Head, Measuring Room dan lainnya,” tutur Rosid seraya menerangkan juga tentang ruang terbuka yang dinamakan Asakai.
“Asakai atau morning meeting ini untuk membahas semua hasil pekerjaan proses produksi dari pagi sampai malam sebelumnya. Aneka perkembangan yang terjadi, baik plus maupun minus disampaikan bersama, antara para line head sampai ke department head. Tentu saja, bahasannya juga mencakup evaluasi dan perbaikan dari hari kemarin, sekaligus apa yang akan dilakukan pada hari ini. Semua laporan yang dibuat, disampaikan bersama dengan menerapkan metode Plan-Do-Check-Action. Penjabarannya, menyangkut laporan tentang permasalahan yang terjadi, faktor penyebabnya, penanggulangan dan tindakan nyata penanganannya,” urai Rosid.
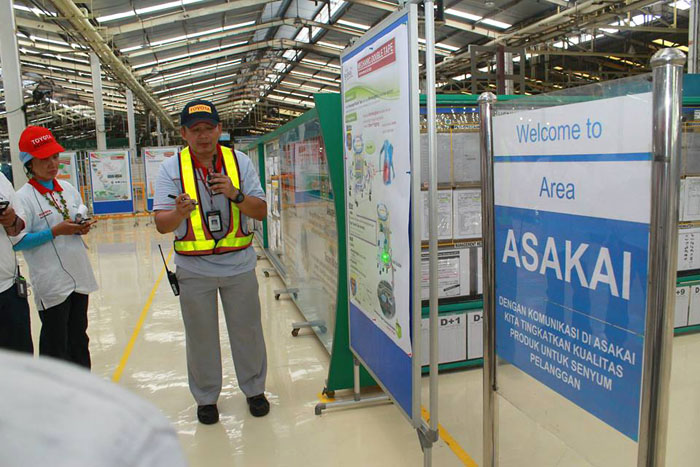
Blusukan di Bagian Ekspor Komponen
Selain melihat langsung bagaimana komponen unit semisal engine untuk mobil Toyota diproduksi, rombongan Kompasiana Visit juga beralih ke sisi pabrik TMMIN berikutnya. Yaitu, Bagian Ekspor Komponen.
Di sini, staf TMMIN, Fathan Ali M menjadi pemandu rombongan.
Dalam paparannya, Fathan menuturkan, tugas bagian ini adalah mengekspor komponen mobil ke mancanegara, khususnya kepada pihak-pihak afiliasi Toyota. “Kita mengekspor komponen vehicle kendaraan tipe Toyota Innova, Fortuner, Yaris, Camry, Etios, dan Corolla. Selain itu, kita juga mengekspor komponen unit engine, maupun engine yang sudah dalam bentuk jadi,” jelasnya.
Secara proses, lanjut Fathan, Bagian Ekspor Komponen mengawali kerjanya dengan menerima barang kiriman dari pihak eksternal yaitu supplier, dan internal semisal dari proses casting, stamping, engine, bahkan dari Pabrik Toyota di Karawang. “Penerimaan part atau barang kiriman ini dilakukan di Receiving Area. Di sini sudah ada tabel yang mengatur kapan jadwal truk pembawa part diperbolehkan masuk. Tidak boleh ada truk masuk yang melanggar jadwal, karena nanti akan membawa dampak pada proses berikutnya. Ini sesuai konsep JUST IN TIME, dimana kita menerima part atau barang, sesuai kebutuhan dan waktunya. Selesai muatan part dari dalam truk di-unloading, maka diteruskan ke Bagian Store,” tutur Fathan penuh semangat.
Selanjutnya, ada proses boxing. “Ini bukan berarti adu tinju, tapi merupakan proses pengepakan (packing). Proses packing bermula sejak 1997. Dan, hingga bulan Mei 2014, kita sudah melakukan ekspor komponen sebanyak 100.000 kontainer,” ungkapnya. “Dari sebanyak 107 supplier yang ada di Toyota Indonesia, ada 59 supplier yang terkait ekspor.”
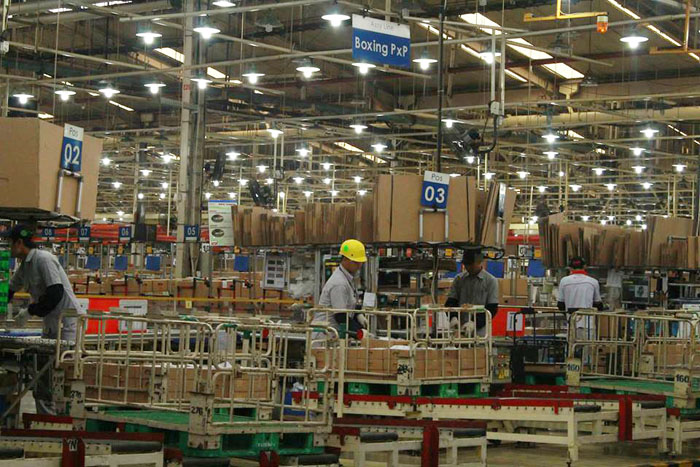
Ada dua tipe proses ekspor pada bagian ini, yaitu pertama, mobil yang sudah utuh dipreteli unit-unitnya, untuk kemudian diekspor. Nantinya, di negara penerima, pihak afiliasi Toyota melakukan perakitan sendiri. Dan kedua, ekspor yang dilakukan part by part komponen sesuai permintaan atau kebutuhan pihak afiliasi Toyota di mancanegara. “Misalnya, mereka hanya meng-order unit spion, ya kita kirim spionnya saja,” ujar Fathan yang nampak gagah dengan seragam kerja warna abu-abu mudanya.
Ekspornya kemana saja?
Fathan menyebut, ada 16 destinasi negara di dunia yang menjadi tujuan ekspor TMMIN. “Terjauh dan terlama pengirimannya adalah Kazakhstan, karena perjalanan transportasi ekspornya butuh waktu 3 bulan. Biasanya, moda transportasi ekspor dilakukan menggunakan kapal laut dan kereta api,” tuturnya. Selain Kazakhstan, negara tujuan ekspor TMMIN lainnya adalah Afrika Selatan, Mesir, Pakistan, India, Malaysia, Thailand, Vietnam, Filipina, Jepang, China, Venezuela, Brasil, Argentina, Australia, dan Taiwan.
Dengan tenggat waktu perjalanan ekspor yang berbulan-bulan itu, TMMIN tidak asal mengirim barang sesuai permintaan begitu saja. Selalu ada parameter dan ukuran kualitas yang diberlakukan.
“Ketika kita mengekspor part ada beberapa tolok ukur. Dan memang, semua yang ada di TMMIN pasti harus terukur, mulai dari Safety, Quality, Productivity, dan Cost. Sehingga untuk memastikan bahwa barang ekspor yang kita kirim sampai di tangan importir dalam kondisi baik, kita tidak begitu saja main kirim barang ekspor. Karena, justru dari kita sendiri sebelumnya sudah harus melakukan Durability Test. Bila hasilnya oke, maka dilanjutkan dengan Logistic Trial, artinya kita menguji pengiriman barang sesuai spesifikasi ke importir. Bila pesanan sudah diterima oleh importir, maka kita melakukan unpack, atau membuka packing secara bersama-sama untuk dilakukan pengukuran soal keamanan, kualitas, produktivitas, dan biayanya. Semua ini penting, karena dalam perjalanan ekspor menggunakan kontainer rawan terjadi kondensasi, akibat suhu di dalam kontainer yang bisa mencapai 70 derajat Celsius. Disinilah tantangan kita, bagaimana menjaga kualitas barang agar tetap dapat berkualitas, meski menjalani perjalanan ekspor yang lama dan butuh perlakuan yang berbeda,” tutur Fathan.
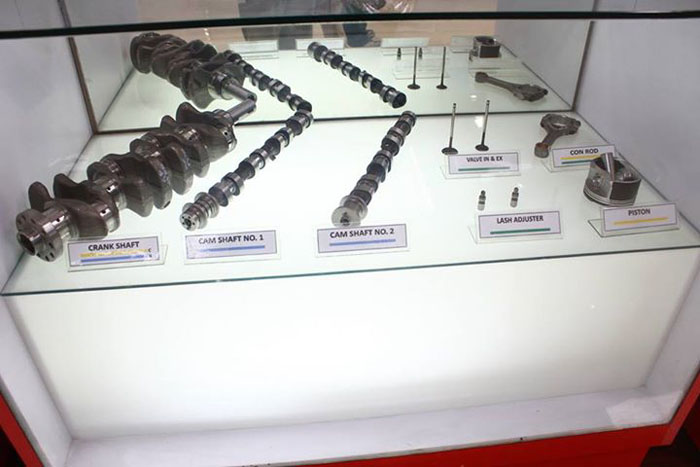
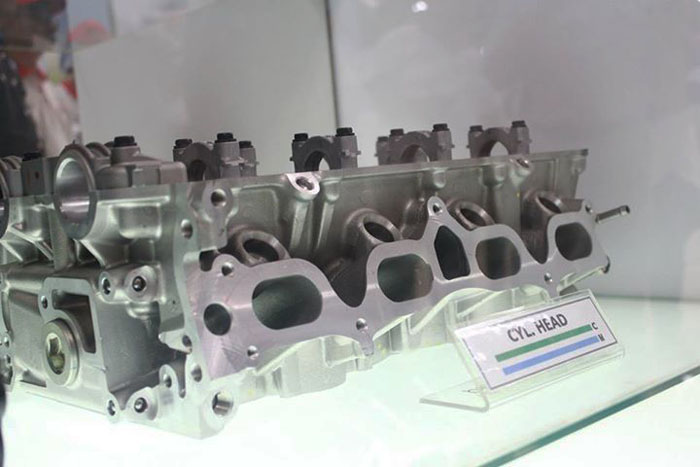
Begitulah, sekilas bagaimana rombongan Kompasianer mengulik Bagian Ekspor Komponen di Pabrik Toyota Sunter 1. Inilah bagian yang juga vital karena merupakan urat nadi yang menghubungkan TMMIN dengan pasar ekspor. Kepercayaan pelanggan jelas menjadi ‘Kartu Truf’ yang dimainkan.
Tak berlebihan bila ada kalimat yang senantiasa dijaga amanatnya, dan ditempelkan sebagai pengingat bersama. Saya beruntung menuliskannya, dan menyampaikan kepada pembaca sekalian.
Kalimat tersebut bertuliskan:
“ONCE WE LOSE CUSTOMER RELIANCE, IT WILL TAKE A LONG TIME TO RECOVERY”.
Sekali kita kehilangan kepercayaan pelanggan, akan butuh waktu lama untuk mengembalikannya.
* * * * *
Baca, tulisan lain:
Baca konten-konten menarik Kompasiana langsung dari smartphone kamu. Follow channel WhatsApp Kompasiana sekarang di sini: https://whatsapp.com/channel/0029VaYjYaL4Spk7WflFYJ2H