Memasuki area pabrik, rombongan dipandu Rosid, staf TMMIN yang mengetahui secara mendalam serba-serbi proses produksi. Pria bertubuh subur dan mengenakan seragam berwarna abu-abu muda ini lebih dulu menjelaskan tentang Toyota Indonesia – History of Manufacturing Products.
“Dari tahun 1985 hingga 2004, pabrik kita sudah memproduksi 13 tipe mesin. Mulai dari tipe 5K untuk Toyota Starlet, 7K untuk Kijang Kapsul, 4A untuk Corolla, 3S untuk Corona, 14D untuk Truk Dyna, 1Z, NZ dan AZ. Sedangkan sejak tahun 2005, kita hanya memproduksi mesin 1 TR dan 2 TR,” tutur Rosid sembari memperlihatkan sejumlah replika mesin tersebut.
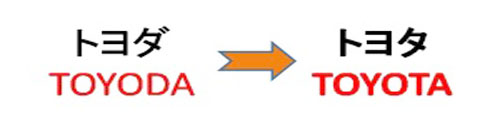
Selama proses produksi berlangsung, Rosid mengatakan, penerapan efisiensi waktu kerja menjadi salah satu yang menjadi perhatian Korporat. “Ini kaitannya dengan man power. Prinsip yang dijalankan adalah bagaimana setiap orang dapat menghargai waktu. Meskipun, hanya mampu mengurangi durasi proses kerja selama satu detik. Tapi, apabila yang cuma satu detik itu bisa di-reduce, maka bila ada berdetik-detik lagi, hasilnya akan menjadi banyak juga waktu kerja (dalam proses produksi) ini yang dapat diefisienkan,” tuturnya.
Efisiensi waktu menjadi salah satu yang sangat penting dalam TPS. Karena, Sistem Produksi Toyota memang senantiasa berusaha meningkatkan profit dengan cara mengeliminasi atau bahkan menghilangkan muda. Muda disini, kerapkali diartikan sebagai waste, pemborosan, dan sesuatu yang tidak memberikan nilai tambah (added value).
Sederhananya begini:
Gerak seorang operator dalam proses produksi, senantiasa terdiri dari Kerja (work) dan Muda (waste). Kerja itu sendiri, terdiri dari gerakan yang menghasilkan nilai tambah, sekaligus gerakan yang tidak menghasilkan nilai tambah.
Ambil contoh, seperti dimuat situs sistemproduksitoyota.com, adalah gerakan memasang tutup ke pulpen. Urutannya, sebagai berikut:
- * Tangan menjangkau pulpen dan tutupnya. (1 detik) … [Tak Punya Nilai Tambah]
- * Tangan mengambil pulpen dan tutupnya. (1 detik) … [Tak Punya Nilai Tambah]
- * Tangan mengarahkan pulpen dan tutupnya. (1 detik) … [Tak Punya Nilai Tambah]
- * Tangan memasang tutup pulpen. (1 detik) … [Punya Nilai Tambah]
- * Tangan meletakkan kembali pulpen. (1 detik) … [Tak Punya Nilai Tambah]
Dari lima kerja yang dilakukan tangan, hanya ada satu proses yang memiliki nilai tambah, yaitu proses nomor 4. Nah, bagaimana mengeliminasi waste adalah berarti bagaimana me-reduce proses urutan kerja dari tangan pada nomor 1, 2, 3, dan 5.

Mengapa ini penting? Sekali lagi, lihat apabila ini dituangkan dalam prosentase. Dari 5 pekerjaan, hanya ada 1 yang memiliki nilai tambah. Maka, perbandingan antara [Pekerjaan yang Punya Nilai Tambah] vs [Pekerjaan yang Tak Punya Nilai Tambah] adalah: 1/5, atau mencapai 20 persen!