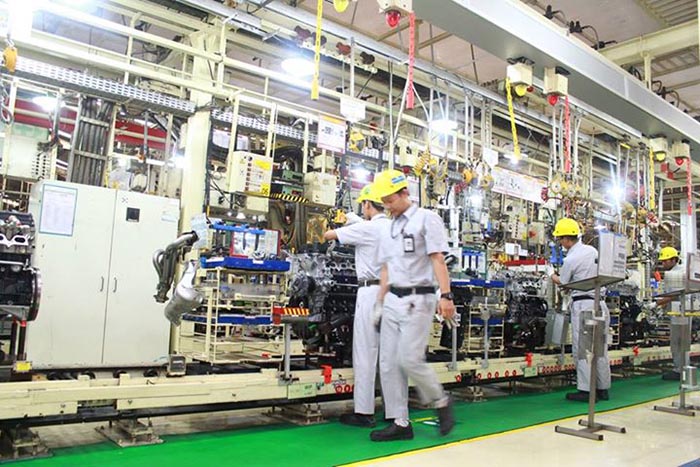
Untuk membuat mobil Toyota, perlu supply chain yang sangat panjang, sehingga dibutuhkan tenaga-tenaga ahli yang memiliki kecakapan skill.
“Karena itu, salah satu semboyan TMMIN adalah ‘We make people first before we make product’. Dengan begitu, setiap plant yang ada di Toyota ini dilengkapi dengan Toyota Learning Center. Dan, yang sedang kita canangkan sekarang adalah aktivitas Clean, Bright, dan Comfort. Clean, tujuannya tidak semata-mata bersih. Tapi dengan bersih, kita bisa dengan mudah menemukan kondisi yang abnormal. Contohnya saja, kalau lantai kita selalu bersih, apabila ada baut yang jatuh, akan segera mudah ditemukan. Bright, bagaimana mengkondisikan agar sinar matahari tetap dapat masuk, sehingga kondisi pabrik menjadi lebih terang, dan karyawan bekerja dengan suasana yang juga lebih enak. Sedangkan Comfort, inilah yang kita kembang terus sehingga operator menjadi mudah untuk bekerja. Misalnya, yang kini tengah dievaluasi adalah mengenai ergonomic, supaya pekerja itu sebagai contoh saja, tidak terlalu banyak membungkuk untuk mengangkat beban berat, dan sebagainya. Inilah yang selalu dievaluasi di TMMIN. Kami yakin, apabila pekerja kita bekerja dengan suasana nyaman, maka pastilah productivity jauh akan meningkat,” tuturnya lengkap.
Selain bergantung dari profesionalisme internal tim, TMMIN juga bergantung dengan area eksternal, dalam hal ini para supplier. Jumlah supplier tidak main-main. Untuk TIER 1 saja, jumlah mereka mencapai 100 supplier. Sedangkan TIER 2 sampai TIER 3, jumlahnya antara 300 hingga 400 supplier.
“Dengan supplier sebanyak itu, bisa kita bayangkan, apabila kita kekurangan suplai satu jenis barang saja, maka dipastikan tidak akan jadi produk mobil. Sehingga kita menganggap, supplier itu sangat penting sekali. Untuk itu, kita harus bantu para supplier ini, caranya dengan men-develop mereka yang ada di TIER 1, melalui activity yang namanya ‘Jishoken’, yang artinya ‘Kaizen’ secara terus-menerus sehingga mereka bisa mandiri untuk melakukan improvement sendiri. Sedangkan untuk supplier pada level TIER 2 dan TIER 3, kita melakukan kolaborasi dengan TIER 1 untuk melakukan pengembangan pada kedua TIER lainnya,” jelas Turmudi.
Contoh improvement, yang dilakukan terhadap para supplier misalnya, dimulai dari presentasi classroom, melakukan assessment sesuai standar kualitas yang ditetapkan, dan pengecekan ke lapangan. “Kalau dulu, barang-barang yang dipasok supplier sekadar ditumpuk begitu saja, sehingga kita tidak tahu berapa jumlahnya, First In First Out (FIFO)-nya bagaimana, dan setelah dilakukan improvement, maka kemudian suplai barang menjadi lebih baik. Karena, kini kita bisa tahu, berapa jumlah barang yang disuplai, berapa maksimum dan minimum level inventory-nya, serta, bagaimana FIFO-nya,” urai Turmudi.
Sunter Plant Overview
Sementara itu, Jatmiko selaku Manager PAD Sunter 1, mempresentasikan Sunter Plant Overview. “TMMIN mempunyai dua area terbesar, Pabrik di Sunter dan Karawang. Untuk yang di Sunter, terdiri dari Sunter 1, Sunter 2, dan Head Office. Sedangkan di Karawang, ada Plant 1 sampai 3,” ujarnya.
Mengenai rekam jejak sejarah Toyota di Indonesia, Jatmiko mengatakan, dibagi menjadi tiga fase. Pertama, ada empat perusahaan yaitu PT Toyota Astra Motor (TAM), PT Multi Astra, PT Toyota Mobilindo, dan PT Toyota Engine. Semuanya beroperasi sejak 1971 hingga 1989. Kedua, keempat perusahaan ini kemudian bergabung menjadi satu yakni PT TAM, pada 1989. Ketiga, sejak 2003 hingga kini, memasuki fase dimana perusahaan dibagi menjadi dua, yakni PT TMMIN dan PT TAM. TMMIN diproyeksikan menangani masalah manufacturer dan eksportir. Sedangkan PT TAM, sebagai distributor dan service part.
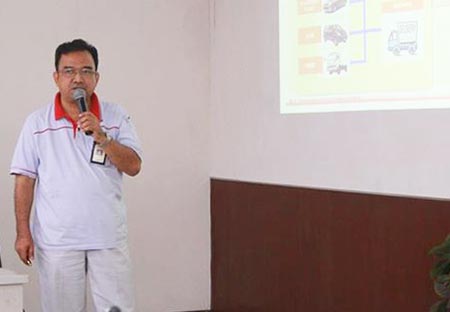
Untuk produksi dan logistik, lanjut Jatmiko, ada supplier yang memasok barang dari impor dan domestik. Setelah ‘masuk’ di Pabrik Sunter 1 dan 2, maka hasilnya kemudian dikirim ke pabrik di Karawang. Barulah kemudian didistribusikan kepada customer. Ada juga yang di-delivery untuk pasar ekspor dan domestik.