Bisa dibayangkan, dengan volume produksi sebanyak itu, dan dengan space area pabrik yang ada, menjadikan sistem Kanban sangat penting dalam memperlancar flow proses dan mengendalikan Inventory in Process.
Sejumlah aturan yang melingkupi sistem Kanban adalah: Memproduksi dan mensuplai barang hanya sesuai dengan jumlah kanban yang diterima; Part/barang harus bergerak bersama Kanban; Tidak memproduksi dan mensuplai tanpa Kanban; dan, Saat pertama part/barang diambil dari boks, Kanban harus diambil dan diletakkan ke pos Kanban.
Sedangkan manfaat pengaturan sistem produksi menggunakan Kanban, ada banyak sekali:
- Memberikan instruksi kerja kepada operator produksi.
- Memudahkan mengontrol kondisi lini produksi.
- Mengetahui kondisi sedini mungkin.
- Mencegah penumpukan barang.
- Secara tidak langsung mencegah kerusakan barang.
- Pengiriman barang sesuai waktu.
- Tepat dalam pengiriman.
- Kelancaran produksi, karena Kanban secara sistem adalah perintah untuk membuat dan mentransportasikan barang.
- Produksi lebih teratur.
- Lokasi kerja lebih teratur
Dengan menerapkan sistem Kanban pula, imbuh Rosid, kondisi di area pabrik menjadi semakin mudah terlihat perkembangannya, tidak saja dari sisi ‘5R’, kualitas, Standard Operation and Procedure (SOP), serta dari penegakan atas aturan-aturan yang berlaku.
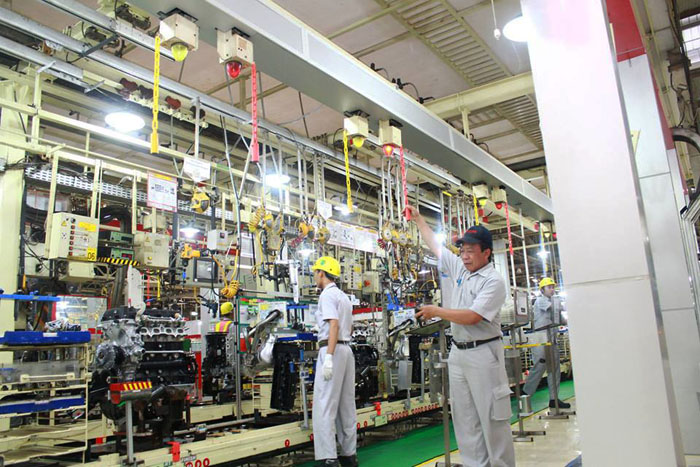
Rosid menyebutkan ‘5R’, apa itu?
Yup! Inilah pakem kerja dalam sistem produksi yang berlaku juga di Pabrik Toyota Sunter 1. Ada yang menyebut ‘5R’, tapi ada juga yang bilang ‘5S’. Lengkapnya, begini:
Pertama, SEIRI atau Ringkas. Merupakan kegiatan memisahkan barang atau material yang diperlukan dan tidak diperlukan, sekaligus menyingkirkan yang tidak diperlukan di area kerja. Dengan demikian, segala barang yang ada di lokasi kerja hanya barang yang benar-benar dibutuhkan dalam aktivitas kerja.
Kedua, SEITON alias Rapi. Bila tidak memenuhi unsur Seiton, maka saat proses produksi dimulai, operator dipastikan bingung mencari dimana letak barang yang diinginkan, sehingga operator harus lebih dulu mencari-cari. Bisa juga terjadi salah menggunakan jig, tool dan lainnya, karena tidak ada identifikasi atau pelabelan. Ekses buruk lainnya adalah pengontrolan area kerja menjadi lebih sulit akibat barang tidak kelihatan jelas.
Ketiga, SEISO atawa Resik. Artinya, mempertahankan kebersihan mesin, peralatan kerja dan tempat kerja dari segala kotoran. Sehingga, segala peralatan kerja tetap terjaga dalam kondisi yang baik. Sudah tentu, SEISO memiliki keuntungan, yaitu area kerja menjadi bersih, sehingga orang yang ada di area tersebut menjadi betah dan nyaman, dan, siapa saja terhindar dari kecelakaan akibat labtai licin oleh minyak pelumas dan sebagainya.
Keempat, SEIKETSU atau Rawat. Maknanya, kegiatan penerapan konsep kebersihan pada diri sendiri dan lingkungan, serta berkesinambungan melaksanakan ketiga langkah sebelumnya, SEIRI, SEITON dan SEISO.